BILLERUD – INDIVIDUELL ANGEPASSTE LÖSUNG
Umstellung auf Hardox® HiAce verbesserte Leistung und Sicherheit
Erfahren Sie, wie der Zellstoff- und Papierhersteller Billerud den Wartungsbedarf reduziert und die Betriebszeit gesteigert hat, nachdem er von unlegiertem Stahl auf korrosionsbeständigen Hardox® HiAce umgestellt hat.
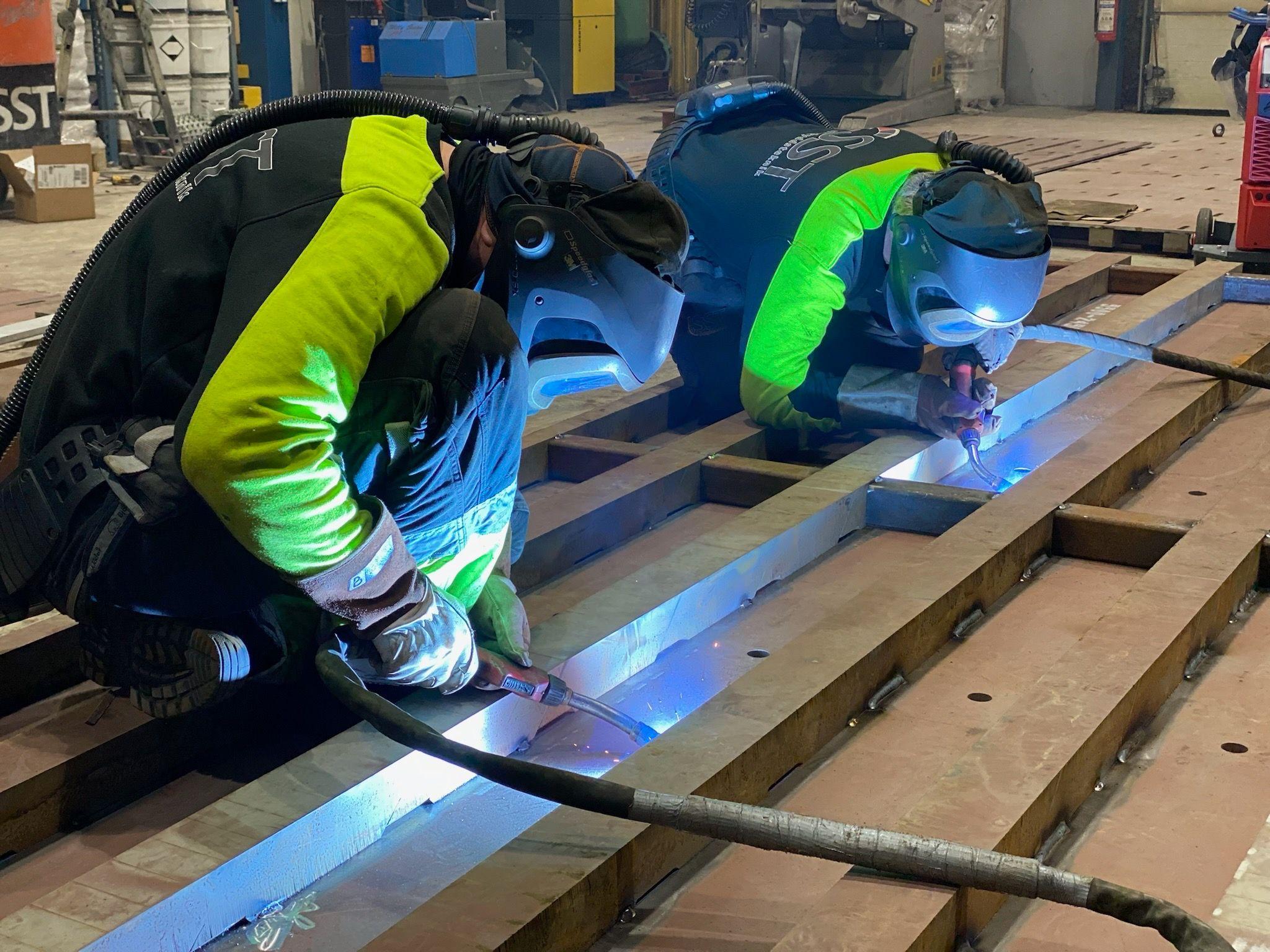
Genug ist genug, meinte man bei Billerud, als das Wartungspersonal immer wieder die Stämme aussortieren musste, die den Holzförderer blockierten. In der Maschine wird das Langholz kontinuierlich von Holztransportern zugeführt und über Ketten, die über Stahlbleche gleiten, in das Werk des Unternehmens gefördert. Das wiederkehrende Problem mit verklemmten Stämmen war durch die alte Konstruktion des Förderbands mit kurzen Blechen bedingt, die sich lösten und verklemmten. Ungeplante Wartungsunterbrechungen, bei denen das Personal die Blockade in schwierigen und gefährlichen Arbeitsschritten beheben musste, verursachten kostspielige Ausfallzeiten. Darüber hinaus war die stark korrosive und saure Umgebung für die bisherige Lösung aus S355-Stahl zu rau.
• Hardox® HiAce ist in einer sauren Umgebung zwei bis drei Mal verschleißfester als ein 400-HB-Stahl
Die neue Lösung, die von Hardox® Wearparts Center Karlstad SST Slitskyddsteknik gebaut wurde, spezifizierte Hardox® HiAce für die Gleitplatten und Kettenführungen, um korrosivem Verschleiß zu widerstehen. SST verwendete auch längere Bleche, um die Anzahl der Verbindungen in den Förderbändern zu minimieren. „Das Ergebnis war großartig: Der Verschleiß war gering, die Oberfläche glatt ohne Risse und das Verschleißmuster der gesamten Oberfläche gleichmäßig“, sagt Anders Nilsson, Wartungsleiter bei Billerud.