REAL STEEL – CUSTOMIZED SOLUTION
Less downtime with Hardox® 600 rotor disc inserts
Learn how switching to Hardox® wear plate helped Real Steel’s customer forget all about uneven wear, time-consuming balancing, and expensive repairs.
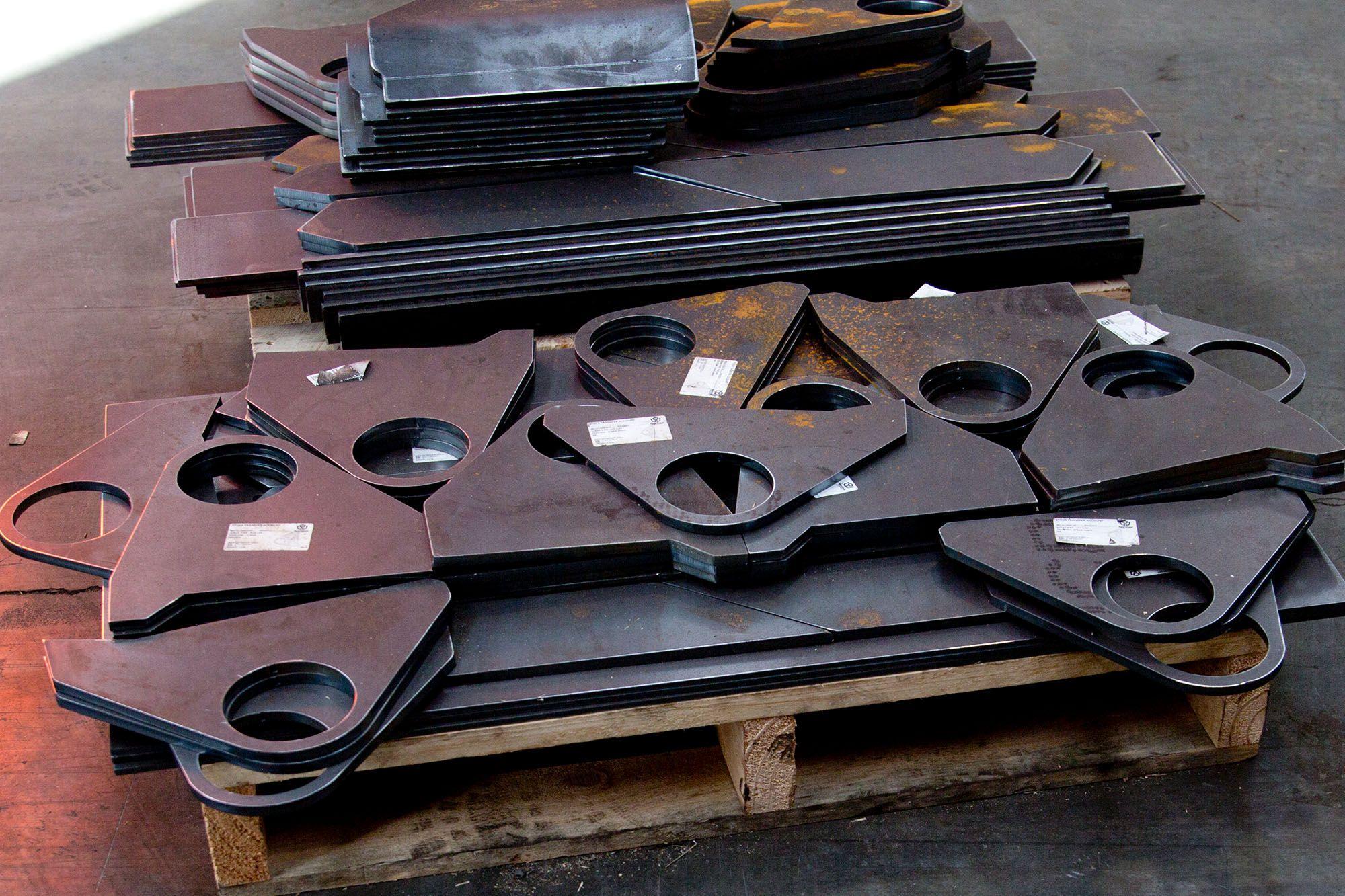
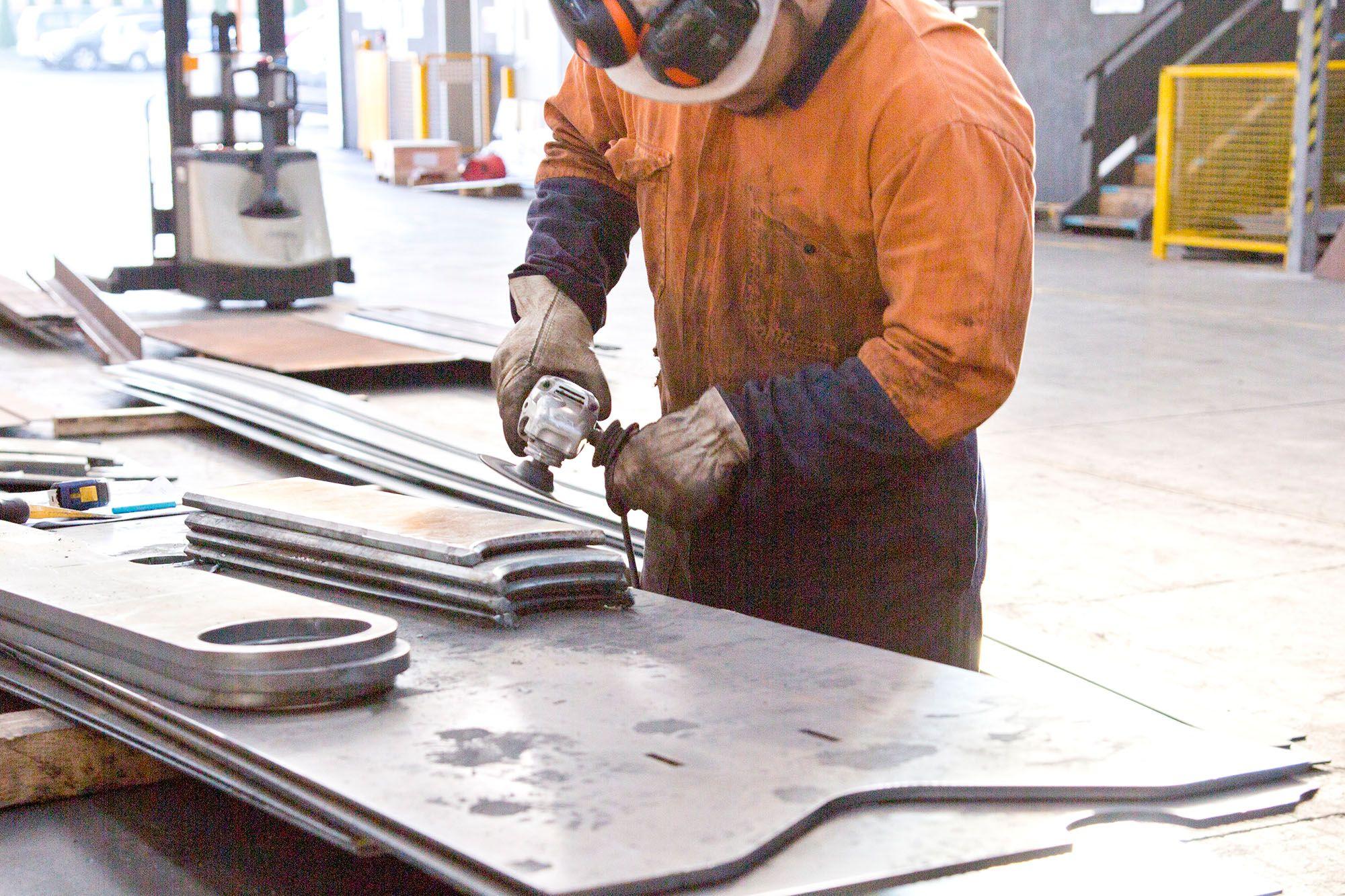
Real Steel is a Hardox® Wearparts center in Wellington, New Zealand. Their customer Sollys Contractors – a transport, construction, and earthmoving service provider – had a problem with their rotor discs wearing out too quickly. They worked together with Real Steal’s wear engineers, who designed a laminated disc with a replaceable insert made from Hardox® 600. The new solution proved to be not only easier to install and more crack resistant; the total wear life of the rotor increased by three times and production costs were reduced by 30 percent.
Real Steel started by upgrading the base plate of the rotor from AR400 to Hardox® 550. Then a recess was machined into the disc to allow for a replaceable Hardox® 600 part to be inserted where the main wear occurred. Real Steal’s Managing Director Luke Mathieson was satisfied with the array of benefits Sollys Contractors experienced. “Our solution created even wear on the rotors and extended the wear life while removing the need for re-balancing the rotors.”
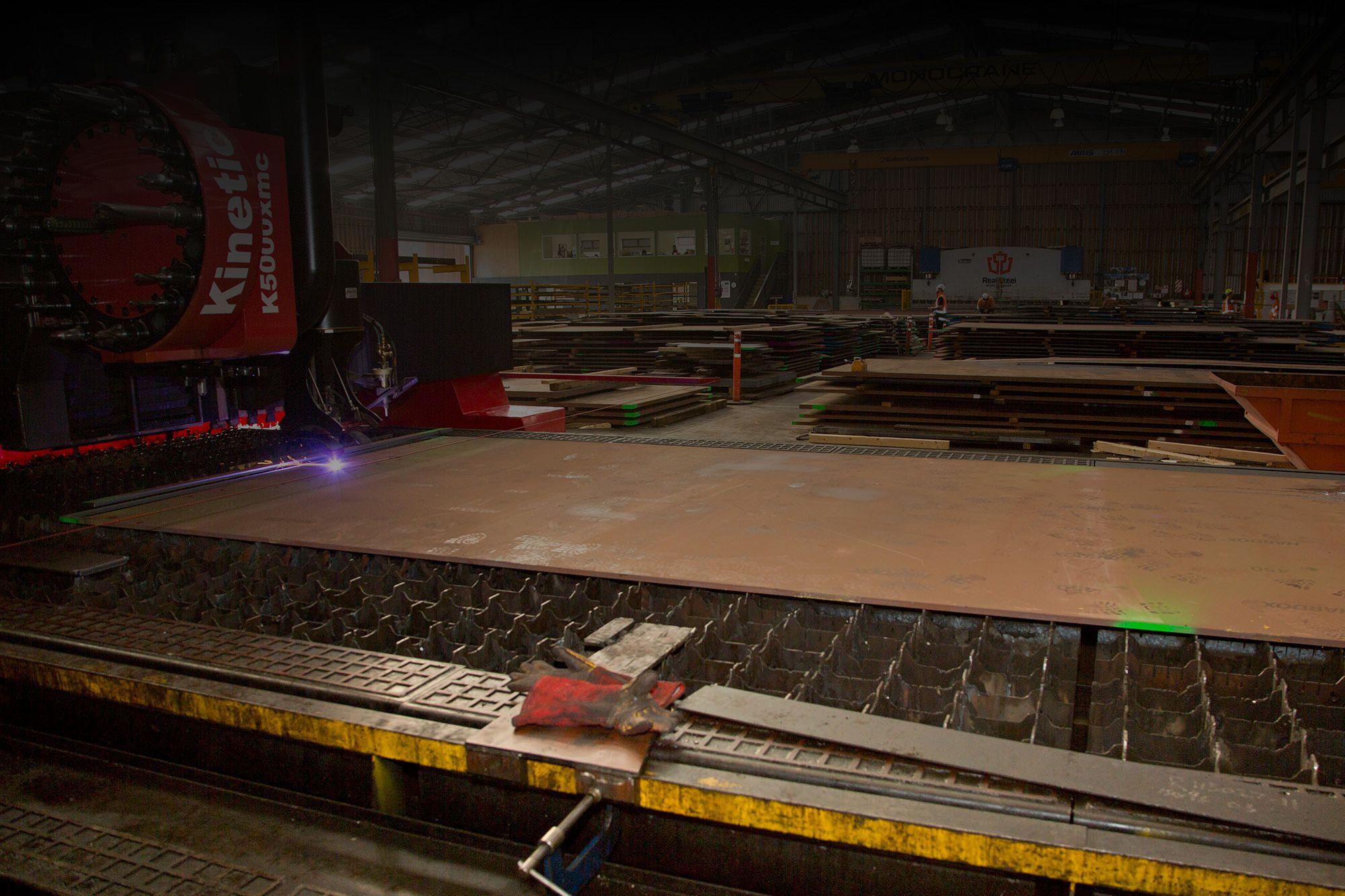
30 % reduced production costs
300 hours of operation before needing minor repair work
3 x longer wear life